L’insieme di micro irregolarità di una superficie nel settore della meccanica viene definito come Rugosità superficiale. Essa si presenta come con un insieme di scalfiture e solchi,
variabili per forma, profondità e direzione.
La rugosità maggiore o minore di una superficie dipende dalla sua finitura superficiale. Questo permette di definire la micro-geometria delle superfici per renderle adatte agli scopi per cui sono
state realizzate.
Rugosità superficiale nelle lavorazioni
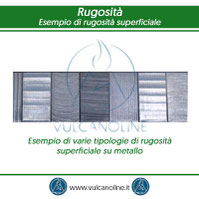
La rugosità superficiale indica la condizione delle superfici lavorate, le quali vengono spesso determinate sommariamente dall'aspetto visivo/tattile dell’oggetto e descritte utilizzando
espressioni come “superficie liscia”, “superficie lucida”, “superficie a specchio”, “superficie ruvida”. Queste differenze nell'aspetto e nella consistenza derivano dalle irregolarità presenti
sulla superficie dell'oggetto.
La precisa determinazione della rugosità superficiale prevede l’adozione di una scala numerica che ne identifica univocamente la condizione che non dipende da una sensazione visiva o
tattile.
Le irregolarità presenti su pezzi e materiali possono essere create intenzionalmente o prodotte da vari fattori come ad esempio levigatura, vibrofinitura o burattatura, processi che creano
irregolarità di diverse forme e dimensioni sovrapposte. La rugosità condiziona anche le prestazioni del prodotto ultimato: un caso da notare è relativo ai componenti di assemblaggio dove la
rugosità influisce in termini di attrito, durata, rumore da funzionamento, consumo di energia e tenuta, incidendo sulla qualità del prodotto e le eventuali lavorazioni successive (applicazioni di
vernici, inchiostri, ecc.)
Motivi per cui viene verificata la rugosità superficiale
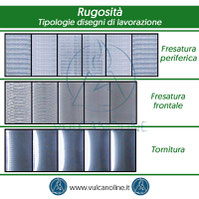
La forma e le dimensioni delle irregolarità risultanti da una superficie lavorata hanno un notevole impatto sulla qualità e sulle prestazioni di tale superficie e sulle prestazioni del prodotto finale. La quantificazione e la gestione delle irregolarità sulla superficie, vale a dire la misurazione della rugosità superficiale, è necessaria per mantenere elevate le prestazioni del prodotto. Quantificare le irregolarità superficiali significa valutarle classificandole per altezza, profondità e intervallo. Vengono quindi analizzati con un metodo predeterminato e calcolati con standard di riferimento. La forma e le dimensioni delle irregolarità superficiali ed il modo in cui verrà utilizzato il prodotto finito determinano se la rugosità superficiale influenza negativamente o positivamente le prestazioni del prodotto. Ad esempio le superfici lavorate verniciate devono facilitare l’adesione della vernice, mentre le superfici di guida devono ruotare facilmente e resistere all'usura. È importante gestire la rugosità superficiale in modo che sia adatta al componente in termini di qualità e prestazioni.
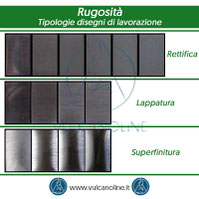
- Usura precoce dei componenti: maggiore è la rugosità superficiale, minore è l’area di contatto effettiva tra le superfici accoppiate, questa situazione può causare usura precoce dei componenti.
- Resistenza alla tensione/sollecitazione dei componenti: formazioni di rugosità come angoli acuti, spazi vuoti e piccole crepe sono molto sensibili alle sollecitazioni/tensioni, influenzando così la resistenza dei componenti.
- Resistenza alla corrosione delle parti: una superficie eccessivamente ruvida può facilmente far penetrare gas corrosivi o liquidi che stagnano nelle valli di rugosità causando l’erosione del materiale.
- Tenuta dei componenti: scarsa adesione tra componenti in cui vi transitano gas o liquidi.
Tipologie di superfici
La superficie è un termine che indica il contorno di un oggetto la quale si pone come limite fra lo spazio esterno e quello occupato dall’oggetto stesso. La superficie viene distinta in tre sottogruppi: reale, geometrica e di riferimento:
- Superficie reale: circoscrive l’oggetto analizzato nel contesto in cui viene collocato per la misurazione.
- Superficie geometrica: determina la superficie dell’oggetto ed è solitamente indicata a disegno o su opportuna documentazione tecnica.
- Superficie di riferimento: determina i parametri e la rugosità dell’oggetto.
Struttura della rugosità superficiale
La forma e le dimensioni di un oggetto sono solitamente indicate a disegno come se la sua superficie potesse essere perfettamente liscia e di una singola forma geometrica. Al contrario qualsiasi
superficie lavorata si distanzia sempre in una certa misura dalla perfezione. Le imperfezioni o irregolarità assumono la forma di colline e valli che possono variare sia in altezza che in
spaziatura, traducendosi in una sorta di "trama" che nell'aspetto e nel tatto è caratteristica del processo di lavorazione e dei suoi difetti associati.
Il controllo della struttura della rugosità superficiale assieme al controllo dimensionale sono di fondamentale importanza poiché i risultati ottenuti influenzano notevolmente la funzione del
componente. La rugosità influisce sulla resistenza all'usura, capacità di carico, durata dell'utensile, resistenza alla corrosione, lubrificazione, resistenza a fatica, capacità di mantenere la
pressione e riduzione del rumore in caso di dispositivi di trasmissione.
Riferimenti normativi struttura della rugosità
Le normative JIS B 0671-1 e ISO 13565-1 si basano sull'analisi utilizzando il metodo dello stilo, la normativa ISO 25178 indica due metodi di valutazione della rugosità: contatto e senza
contatto.
Adottare un doppio metodo aiuta a risolvere problematiche derivanti dalle variazioni dei risultati delle rilevazioni in base all’area di misura e variazioni dovute alla direzione di scansione.
Geometria del profilo di rugosità
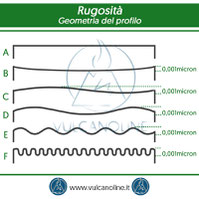
La figura a lato mostra la forma di rugosità, come un profilo inizialmente liscio derivi in un profilo finale alterato a causa delle imperfezioni strumentali:
Il punto A rappresenta la sezione trasversale di una superficie teoricamente liscia e piana (superficie perfetta).
I punti B e C rappresentano errori di "forma".
I punti D e E rappresentano ondulazioni/lunghezze d’onda.
Il punto F rappresenta la “vera” rugosità superficiale. Chiamata "struttura primaria" essa è causata dall'azione dello strumento da taglio utilizzato per lavorare la superficie.
L'ondulazione è denominata "struttura secondaria" ed è causata ad esempio dalle “imperfezioni” della macchina utensile da taglio, come ad esempio vibrazioni derivanti da strumenti mal
regolati.
Le imperfezioni che si trovano su una qualsiasi superficie assumono generalmente la forma di picchi e valli di rugosità di varia altezza e larghezza; esse sono una caratteristica del processo
utilizzato per produrre l’oggetto. Una superficie solitamente è costituita da molte lunghezze d'onda diverse: alcune risultanti dall'avanzamento dello strumento deputato alla lavorazione mentre
altre sono causate dall'effettiva azione di taglio. Inoltre alcune lunghezze d'onda possono essere prodotte dalle vibrazioni.
Cause di imperfezioni e rugosità superficiale
Tipo di imperfezione | Problema correlato o Causa di errore |
Errore di forma | Errori di forma derivanti da problematiche durante il processo di lavorazione, come ad esempio errori nelle modalità di utilizzo delle macchine utensili, guide, mandrini, bloccaggio insufficiente, allineamento impreciso, usura irregolare delle attrezzature. |
Struttura della superficie | La struttura della superficie include rugosità, ondulazione e posizione, vale a dire le deviazioni che sono più corte nella lunghezza d'onda rispetto alle deviazioni dell'errore di forma. |
Rugosità (struttura primaria) | La rugosità indicata come "deviazione micro-geometrica" o "irregolarità micro-geometriche" è definita all’interno dell'area, dove vengono eliminate le deviazioni di forma e ondulazione. |
Ondulazione (struttura secondaria) | Può essere causata da vibrazioni, trattamenti termici o deformazioni. L'ondulazione è la componente della rugosità. |
Difetti | I difetti sono problemi involontari e indesiderati rinvenibili su una superficie. Tali imperfezioni sono graffi, buchi, crepe, cavità, controlli, porosità ecc. Questi possono essere osservati direttamente o con l'ausilio di liquidi penetranti o altri materiali che li rendono visibili per l'esame e la valutazione. |
Picchi, valli ed altri termini inerenti al profilo di rugosità
La rugosità è formata da una serie di parametri come picchi e valli irregolari che ne compongono la superficie. Essi possono essere così definiti:
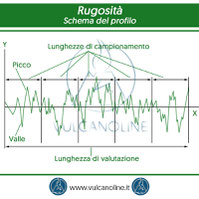
- Scostamento del profilo: lo scostamento del profilo è la distanza fra un punto del profilo e la linea di riferimento, letta nella stessa direzione di misura.
- Linea di riferimento: come linea di riferimento possono essere prese in esame due modalità. La prima è la linea media dei minimi quadrati del profilo (o linea media), essa ha la forma del profilo geometrico e divide il profilo in modo che, all'interno della lunghezza di base "l", la somma dei quadrati degli scostamenti a partire da questa linea sia la minima. In pratica, questo viene fatto con un profilo digitalizzato. L'applicazione più comune di una linea media dei minimi quadrati è quella di "livellare" il profilo tracciato grezzo. Un filtro indica che la linea è la linea media implicita in un filtro del profilo. Ad esempio, il profilo di ondulazione può essere considerato la linea media del profilo di trama. Un altro nome per la linea media del filtro negli strumenti analogici è la "linea media elettrica". La seconda è la linea media aritmetica del profilo (o linea centrale), essa ha la forma del profilo geometrico ed è parallela alla sua direzione. Divide il profilo in modo che, all'interno della lunghezza di base, la somma delle aree F e di quelle F' comprese fra la linea centrale ed il profilo siano uguali.
- Altezza del profilo: l'altezza del profilo è la distanza del profilo dalla linea media. L'altezza del profilo è considerata positiva sopra la linea media e negativa sotto la linea media.
- Picco di profilo: un picco di profilo è una porzione del profilo che si trova al di sopra della linea media e congiunge la linea media a ciascuna estremità. L'altezza di un picco è riferita al punto più alto del picco del profilo.
- Valle del profilo: una valle del profilo (analoga al picco di un profilo) è una porzione del profilo che si trova al di sotto della linea media e la congiunge a ciascuna estremità. La profondità di una valle è riferita al punto più basso all'interno della valle del profilo.
- Irregolarità del profilo: un picco del profilo ed una valle del profilo adiacente costituiscono una irregolarità del profilo.
- Picco locale del profilo: un picco locale del profilo è una porzione del profilo che unisce due minimi locali successivi del profilo.
- Valle locale del profilo: una valle locale è una porzione del profilo che congiunge due massimi locali (due "punti alti") successivi del profilo tra successivi (massimi locali) nel profilo e si trova tra due massimi (sopra o sotto la linea media).
- Irregolarità locale: Un picco locale e la sua valle adiacente costituiscono una irregolarità locale.
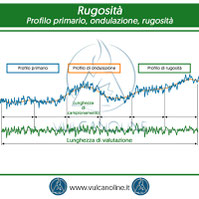
- Profilo primario: Il profilo primario è una curva in cui un filtro passa-basso di compensazione di fase del cut-off λs viene applicato al profilo totale.
- Profilo di ondulazione: Il profilo di ondulazione indica una curva in cui il filtro di compensazione di fase di cut-off λf e λc è applicato al profilo primario.
- Profilo di rugosità: Il profilo di rugosità si riferisce a una curva in cui solo le componenti ad alta frequenza del profilo primario vengono registrate utilizzando un filtro passa-alto di compensazione di fase (cut-off λc).
- Cut-off: Il cut-off è un filtro che analizza solo le lunghezze d’onda di interesse. Per i parametri di superficie solitamente vengono analizzate le lunghezze d'onda tra un cut-off superiore e uno inferiore: questi sono indicati come Ls o λs (il più corto) e Lc o λc (il più lungo). Il termine “Cut off" viene utilizzato anche come sinonimo di lunghezza di campionamento poiché essa solitamente è impostata su Lc.
- Lunghezza di campionamento: I parametri di rugosità sono determinati in base alla suddivisione in lunghezze del profilo. Queste lunghezze sono chiamate lunghezze di campionamento. La lunghezza di campionamento (l) è lunga a sufficienza per includere un quantitativo di dati sufficiente a comporre un’analisi.
- Lunghezza di valutazione: La lunghezza di valutazione si riferisce alla parte di una data lunghezza estratta dal profilo lungo la direzione dell’asse X, al fine di determinare la deviazione media aritmetica e altri parametri di rugosità. La lunghezza di valutazione contiene una o più lunghezze di campionamento (lo standard è 5 lunghezze di campionamento). Relativamente ai profili primari la lunghezza di valutazione corrisponde alla lunghezza di campionamento.
Lunghezze di misura del profilo di rugosità
La lunghezza di valutazione è la porzione del profilo di rugosità misurata in direzione parallela all’andamento generale del profilo. Essa è necessaria per la valutazione dei parametri di rugosità superficiale. La lunghezza di valutazione può includere una o più lunghezze di campionamento. La lunghezza di campionamento è l'intera lunghezza di un profilo necessaria per la valutazione delle irregolarità da prendere in considerazione su cui sono stati raccolti i dati.
Unità di misura rugosità
Nel sistema internazionale l'unità di misura della rugosità è il micrometro o micron (1 micron = 1micra = 0,000001 m = 0,001 mm), mentre nel
sistema anglosassone viene utilizzato il micropollici (μ ").
Questa misura è indicata nei disegni parti costruttive da segni e valori numerici, secondo gli standard di rugosità di qualità esistenti, che variano da paese a paese.
Solchi di rugosità (pattern o disegni di lavorazione)
Il metodo di lavorazione utilizzato determina normalmente la direzione del solco di rugosità (disegno o pattern) predominante visibile sulla superficie.
I processi di lavorazione come tornitura, fresatura, foratura e rettifica imprimono sulla superficie una serie di striature ed incisioni marcate nella direzione in cui lo strumento sta operando.
Altri processi, invece, come la sabbiatura producono superfici senza una direzione caratteristica.
I solchi di rugosità possono risultare di molteplici aspetti:
- Paralleli o Unidirezionali (II): i solchi risultano disposti in un disegno ordinato, paralleli al piano di proiezione della vista.
- Perpendicolari: i solchi risultano disposti in un disegno ordinato, ortogonali al piano di proiezione della vista.
- Croce (X): i solchi risultano disposti in un disegno ordinato, incrociato in due direzioni, oblique al piano di proiezione della vista.
- Multidirezionale (M): i solchi risultano disposti in un disegno multidirezionale senza un ordine geometrico preciso.
- Circolari (C): i solchi risultano disposti in un disegno ordinato, approssimativamente circolari rispetto al centro della superficie sulla quale è applicato il disegno di lavorazione. Un esempio di lavorazione da cui deriva questa tipologia di solco è la tornitura.
- Radiali (R): i solchi risultano disposti in un disegno ordinato, approssimativamente radiali rispetto al centro della superficie sulla quale è applicato il disegno di lavorazione.
- Puntiforme (P): i solchi risultano essere ad andamento particolare non orientati verso una direzione particolare, ne sporgenti. Un esempio di lavorazione da cui deriva questa tipologia di solco è la sabbiatura.
Nota: Se è necessario è possibile specificare un motivo di superficie che non è chiaramente definito da questi simboli, questo deve essere ottenuto aggiungendo una nota adatta al disegno.
Metodi di misurazione della rugosità superficiale
La rugosità superficiale non può essere facilmente definita utilizzando un singolo parametro ma un insieme di parametri che ne caratterizzano la superficie. I metodi disponibili per misurare questi parametri e quindi la rugosità delle parti lavorate possono essere classificati in due tipologie:
- Metodi indiretti o di confronto: la rugosità superficiale viene confrontata con una superficie standard/master di riferimento, come ad esempio i comparatori di rugosità visivi o tattili.
- Metodi diretti: la rugosità superficiale viene misurata con strumenti a contatto/ottici come ad esempio i rugosimetri con stilo.
Misurazione della rugosità tramite metodi indiretti o di confronto
Utilizzando i metodi di confronto per stabilire il grado di rugosità si effettua una valutazione mediante l’osservazione e la prova tattile della superficie ispezionata con uno standard di
riferimento. Questi metodi sono caratterizzati da un elevato margine di errore, oltre a questo l’operatore deve avere esperienza per effettuare una valutazione corretta.
Nella tabella che segue analizziamo alcuni metodi di confronto e i vantaggi e svantaggi nell’utilizzo.
Nome del metodo | Principio di funzionamento | Vantaggi | Svantaggi | Osservazioni |
Ispezione tattile | La punta del dito viene passata lungo la superficie ad una velocità di 25-30 mm al secondo e la stessa operazione è successivamente effettuata su blocchi di rugosità nota. | Metodo semplice ed economico | Difficile valutare il grado di rugosità e rilevare i piccoli difetti. I risultati spesso sono soggettivi. L’operatore deve essere esperto. | Si possono rilevare irregolarità fino a 0,0125 mm circa |
Ispezione visiva | L'ispezione è effettuata ad occhio nudo e confrontata con blocchi di rugosità di riferimento | Metodo semplice ed economico | L'uso è limitato solitamente a superfici più ruvide. I risultati spesso sono soggettivi. L’operatore deve essere esperto. | L’ispezione può essere eseguita utilizzando lenti di ingrandimento illuminate per migliorare la valutazione |
Ispezione dei graffi | Materiale morbido come gomma o plastica viene strofinato sulla superficie | Metodo semplice ed economico | Il metodo potrebbe danneggiare la superficie delicata. Poca accuratezza. | I graffi formati sulle superfici dei materiali morbidi vengono visionati e utilizzati per confronto |
Riflesso di luce | La luce riflessa dalla superficie viene misurata da una fotocellula e confrontata con le letture già calibrate | Metodo abbastanza semplice ed economico | Il tempo richiesto per misurare la superficie è più lungo | Per un corretto confronto sono necessarie più superfici con rugosità nota |
Metodo di sezionamento |
Una porzione del campione viene tagliata ed esaminata | Metodo molto accurato | Metodo distruttivo e costoso | Esame effettuato al microscopio ottico |
Misurazione della brillantezza |
La variazione della brillantezza è giudicata sia dall’occhio umano sia da appositi strumenti (esempio glossmetri). | Metodo abbastanza semplice | Il risultato può essere fuorviante. La strumentazione per la misura della brillantezza è costosa. | Il rapporto tra rugosità e brillantezza allo stato grezzo è inversamente proporzionale |
Replica di rugosità | Se la superficie non è accessibile alla sonda dello strumento (con metodo diretto) viene creata una replica della superficie e confrontata. | Utilizzando alcune tecniche moderne, resine epossidiche o altre resine, è possibile ottenere una fedeltà di replica al 100%. | In molti casi, per fattori tecnici, la replica è fedele all’originale in misura dell'80% | Il composto viene premuto contro la superficie finché non si indurisce |
Misurazione della rugosità tramite metodi diretti
I metodi diretti per la misurazione della rugosità superficiale si avvalgono solitamente di strumenti chiamati rugosimetri, grazie ai quali è possibile verificare il rispetto delle parti
lavorate alle principali norme di rugosità.
In commercio esistono molte tipologie di rugosimetri, i modelli più utilizzati nelle lavorazioni industriali sul campo
sono prevalentemente di due tipologie: i rugosimetri portatili con tastatore stilo a scorrimento come ad esempio il rugosimetro modello VLRGX6210, oppure rugosimetri a singolo punto come ad esempio il rugosimetro modello VLRGSB6233.
Il rugosimetro a scorrimento (o carrello) è composto da un tastatore che può essere induttivo (il più utilizzato), il quale è dotato di uno stilo che scorrendo esamina la rugosità lungo la linea
di valutazione della porzione di campione presa in esame, oppure di tipo ottico il quale grazie ad un sensore verifica la rugosità lungo la linea di valutazione della porzione di campione presa
in esame analizzando le variazioni di posizione del raggio riflesso sulla superficie. Il tastatore di tipo ottico non operando meccanicamente riesce a penetrare con molta più efficienza nelle
valli di rugosità ed individuare con maggior precisione le dimensioni della punta del picco. I rugosimetri con tastatore sono dotati di unità di traslazione che ha il compito di muovere il
tastatore. Solitamente questa tipologia di rugosimetro ha all’interno un’unità centrale che gestisce la movimentazione del tastatore e la conversione da segnale analogico (se si utilizza un
tastatore induttivo tipo stilo) a digitale.
L’unità centrale del rugosimetro si occupa anche di calcolare i parametri di rugosità precedentemente selezionati e previsti dal rugosimetro, come ad esempio Ra, Rq, Rz, Rt. Questi parametri sono
importanti poiché da essi si può verificare il buon esito di un lavoro come ad esempio nel settore della verniciatura, dove si opera con un preciso grado di sabbiatura come ad esempio la sabbiatura SA
2.5 che richiede una rugosità specifica del pezzo.
La misura della rugosità espressa in Ra (come per gli altri parametri che verranno di seguito introdotti) normalmente si esegue rilevando il profilo lungo un certo numero di lunghezze di base L.
La somma delle lunghezze di base rilevate rappresenta la lunghezza di valutazione (Ln). La lunghezza di valutazione solitamente è pari a cinque volte la lunghezza di base.
Tabella della lunghezza di base e della lunghezza di valutazione in funzione della rugosità Ra | |||
Valore Ra | Lunghezza di base (l) mm | Lunghezza di valutazione (ln) mm | |
0,006-0,02 | 0,08 | 0,4 | |
0,02-0,10 | 0,25 | 1,25 | |
0,1-2,0 | 0,8 | 4,0 | |
2,0-10,0 | 2,5 | 12,5 | |
10,0-80,0 | 8,0 | 40,0 |
I rugosimetri a singolo punto sono caratterizzati da una struttura meno complessa rispetto a quella dei rugosimetri con tastatore a scorrimento: dotati di una sonda integrata o esterna composta
da una punta acuminata hanno una struttura simile a quella dei durometri shore. Essi esaminano la massima profondità
di rugosità raggiunta grazie alla pressione esercitata da una punta acuminata la quale penetra all’interno della valle di rugosità calcolando su singolo punto l’altezza della cresta.
Analizzando la superficie in solo punto del campione questi strumenti sono privi di unità di calcolo dei parametri di rugosità standard. Il dato rilevato è quindi una misura di altezza di
rugosità equiparabile alla rilevazione effettuata utilizzando un calibro di profondità, chiaramente rapportato a dimensioni ridotte e con la conseguente adozione di unità di misura espressa in
micron.
Parametri di rugosità
I parametri di rugosità che andremo a trattare possono essere separati in tre tipologie di base: Ampiezza, Spaziali e Ibridi.
- I parametri di ampiezza sono misure di caratteristiche verticali delle deviazioni della superficie sulla linea di valutazione.
- I parametri di spaziatura sono misure di caratteristiche orizzontali delle deviazioni della superficie sulla linea di valutazione.
- I parametri ibridi sono misure in combinazione sia su parametri spaziali che su parametri di ampiezza sulla linea di valutazione.
Per le tre categorie elencate vi sono anche i corrispondenti parametri relativi al profilo di ondulazione ed il profilo primario, che in questo articolo non approfondiremo.
I parametri di riferimento più conosciuti nelle lavorazioni meccaniche sono gli standard di rugosità Ra, Rz, Rt, Rq, Rms.
Per quanto riguarda gli altri parametri di rugosità è possibile collocarli nelle seguenti categorie:
- Parametri di rugosità di ampiezza (picchi e valli) Rp, Rv, Rc.
- Parametri di rugosità medi di ampiezza Rsk, Rku.
Tabella comparativa parametri e profili | ||||
Parametri | Profili | Definizione | ||
Primario | Ondulazione | Rugosità | ||
Ampiezza (picchi e valli) | Pp | Wp | Rp | Massima altezza di picco del profilo |
Pv | Wv | Rv | Massima profonditò di valle del profilo | |
Pz | Wz | Rz | Massima altezza del profilo | |
Pc | Wc | Rc | Altezza media degli elementi del profilo | |
Pt | Wt | Rt | Altezza totale del profilo | |
Ampiezza (media ordinate) | Pa | Wa | Ra | Scostamento medio aritmetico del profilo |
Pq | Wq | Rq | Scostamento quadratico medio del profilo | |
Psk | Wsk | Rsk | Asimmetria (Skewness) | |
Pku | Wku | Rku | Appiattimento (Kurtosis) | |
Lunghezza d'onda | PSm | WSm | RSm | Lunghezza media degli elementi del profilo |
Ibridi | PΔq | WΔq | RΔq | Pendenza quadratica media del profilo |
Relativi a curve | Pmr(c) | Wmr(c) | Rmr(c) | Percentuale della lunghezza portante |
Pδc | Wδc | Rδc | Differenza di altezza della sezione | |
Pmr | Wmr | Rmr | Percentuale della lunghezza portante relativa |
Valutazione delle misure di rugosità riferimento normativa EN ISO 4288
I valori di misurazione della rugosità, in particolare i parametri Rt, Rz, Rz1max e Ra, variano in un intervallo compreso tra -20% e + 30%. Pertanto, una singola misurazione può non fornire un
quadro completo della conformità con i parametri tollerati. Nell'allegato A della norma DIN EN ISO 4288 è prevista la seguente procedura:
Regola del massimo
Tutti i parametri di rugosità con il suffisso "max" (ad esempio Rzmax) rappresentano il valore medio massimo misurato all'interno delle cinque lunghezze di campionamento. La misurazione dovrebbe
essere effettuata in tre posizioni, almeno, sulla superficie in cui si possono prevedere i valori massimi; in nessuna posizione deve superare il valore specificato nella tolleranza.
Regola del 16%
Tutti i parametri di rugosità senza il suffisso "max" rappresentano il valore medio misurato all'interno delle cinque lunghezze di campionamento: il 16% dei valori misurati possono essere
superiori alla tolleranza specificata.
Metodo di valutazione progressivo:
1. Se il primo valore misurato è inferiore al 70% del limite, questo è considerato conforme.
2. In caso contrario, effettuare altre due misurazioni in altri punti sulla superficie; se tutti e tre i valori misurati sono inferiori al limite, questo è considerato conforme.
3. In caso contrario, effettuare nove misurazioni aggiuntive in altri punti sulla superficie; se in totale non più di due valori misurati sono superiori al limite, questo è considerato conforme.
Copyright by © Vulcanoline All rights reserved