Introduzione alla calibrazione
Misurare lo spessore dei materiali è un’esigenza comune per la maggior parte dei settori produttivi, poiché la qualità ed il periodo di vita di un manufatto lavorato dipendono dalle corrette
misure e verifiche effettuate sia in sede preliminare che su prodotto finito. Molto spesso i materiali lavorati ed in lavorazione non consentono verifiche con metodi classici (calibri,
micrometri, ecc) e tantomeno possono subire prove invasive al fine di verificarne lo spessore. Per ovviare a questo problema sono disponibili strumenti che sfruttano gli ultrasuoni per la
determinazione dello spessore del materiale, questi strumenti si chiamano spessimetri ad ultrasuoni.
In relazione a questi spessimetri ad ultrasuoni sorge la problematica di garantire la tracciabilità e la
corretta misurazione dello spessore di ogni materiale misurato. Questo significa che il risultato derivante dalla misura deve essere correlato ad una precedente calibrazione dello strumento.
Definizione di calibrazione spessimetro ad ultrasuoni
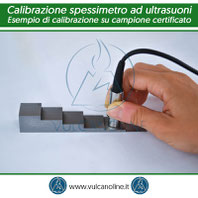
La calibrazione dello spessimetro ad ultrasuoni è un’operazione che fornisce la relazione tra la lettura dello strumento ed il valore dello spessore del materiale analizzato, settando la corretta velocità di propagazione del suono.
Uno spessimetro ad ultrasuoni riesce a leggere lo spessore di un campione analizzando il tempo impiegato dalle onde ad ultrasuoni durante la propagazione nel materiale ed il successivo eco di ritorno. Per trasformare questa misura temporale in misurazione dello spessore, lo spessimetro ad ultrasuoni deve essere impostato selezionando la corretta velocità di propagazione del suono nel materiale di prova, il punto zero, la tipologia di sonda e le caratteristiche dell’onda. Questa procedura è indicata come calibrazione dello spessimetro ad ultrasuoni. L’operazione di misura, richiede l’utilizzo di un “accoppiante” il quale funge da tramite tra sonda e superficie, i più comuni accoppianti sono ad esempio l’apposito gel per ultrasuoni, pasta o liquidi come olio e glicerina.
Gli spessimetri ad ultrasuoni vengono comunemente calibrati e controllati utilizzando appositi campioni di riferimento commerciali di spessore noto, come ad esempio il master 6 step di calibrazione in acciaio, il cui valore è riportato su ogni gradino. In alternativa
è possibile calibrare lo strumento su campioni appositamente realizzati utilizzando il medesimo materiale del campione oggetto di test.
Numerosi fattori come l’utilizzo prolungato, usura e condizioni ambientali influiscono negativamente sulle prestazioni dello strumento, un programma periodico di calibrazione e verifica dello
spessimetro consente di mantenere una costante di precisione e ripetibilità. È molto importante programmare una calibrazione ogni volta che il materiale di prova, la sonda o la temperatura del
materiale subiscono una variazione significativa. Inoltre sono consigliati controlli periodici della strumentazione tramite campioni di spessore di valore noto per verificare che il misuratore di
spessore ad ultrasuoni funzioni correttamente, soprattutto per applicazioni in condizioni difficili.
La precisione delle misure rilevate con spessimetri ad ultrasuoni è dipesa dalla corretta calibrazione dello strumento. Una errata calibrazione provocherà letture di spessore imprecise o falsate.
Fortunatamente la calibrazione è un processo solitamente semplice.
Molti spessimetri ad ultrasuoni adottano funzioni di calibrazione memorizzabili che possono essere richiamate ed utilizzate rapidamente in caso di necessità, come ad esempio lo spessimetro ad ultrasuoni modello VLSTC2000, in grado di memorizzare un gran numero di velocità di
propagazione del suono, rapidamente selezionabili. Questo strumento è ampiamente utilizzato durante il controllo ad
ultrasuoni delle lamiere, su cisterne, silos, pali e molto altro ancora.
Settaggio velocità di propagazione del suono e punti di calibrazione
La calibrazione di uno spessimetro ad ultrasuoni prevede alcuni step per settare e memorizzare la corretta velocità di propagazione del suono e per eliminare eventuali falsi segnali rilevati
dello strumento.
Durante la calibrazione su punto zero viene fornito allo spessimetro ad ultrasuoni un valore zero che compensa la porzione del tempo di transito dell'impulso che rappresenta fattori diversi dal
percorso effettivo del suono nel pezzo di prova. I principali fattori inclusi nel valore zero sono i ritardi elettronici dello spessimetro, il ritardo derivato dai cavi, dal tipo di sonda e
dall’accoppiamento. Nel caso di sonde a contatto ad esempio il ritardo del trasduttore comprende la quantità di tempo necessario perché l’onda sonora esca dal trasduttore attraverso il suo
dispositivo antiusura.
La calibrazione più comunemente utilizzata dalla maggior parte degli spessimetri ad ultrasuoni di fascia media è la calibrazione ad un punto che consente di impostare lo strumento su di un
preciso spessore di valore noto ed il settaggio della relativa velocità del suono.
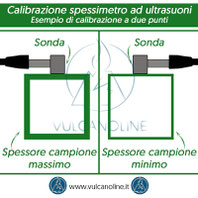
La procedura di calibrazione raccomandata, se lo strumento lo prevede, è una calibrazione a due punti, che richiede due campioni del medesimo materiale di prova di differenti spessori, all'interno dell'intervallo di spessore da misurare e i cui spessori sono noti con precisione. Questi non devono essere necessariamente blocchi di test commerciali, purché il loro spessore sia noto. È molto più importante che il materiale utilizzato per la calibrazione sia esattamente uguale al materiale da misurare e che abbia idealmente la stessa finitura superficiale e la stessa geometria. Facendo un esempio pratico nel caso in cui si necessiti di misurare pezzi che vanno da 3 a 5mm è consigliata la calibrazione a due punti su campioni da 2mm e da 7mm, della medesima tipologia di materiale e geometria dei pezzi oggetto di test. Seguendo l’operazione di calibrazione a due punti è buona norma controllare le letture su uno o più campioni standard di riferimento aggiuntivi il cui spessore si trova tra i valori utilizzati per la calibrazione. L'accoppiamento o l'inserimento numerico errati causano errori così come l'uso di standard di calibrazione il cui spessore è al di fuori dell'intervallo di misurazione valido per un dato spessimetro, trasduttore e funzione.
Se la lettura dello spessore non è corretta o aumenta all'aumentare dello spessore, l'errore si trova molto probabilmente nel valore di velocità di propagazione impostato. Se il valore di
spessore letto non è stabile su più misurazioni effettuate nel medesimo punto allora l'errore molto probabilmente è da imputare nella calibrazione del punto zero. In entrambi i casi il processo
di calibrazione a due punti deve essere ripetuto.
Durante la calibrazione si deve ricordare che i principali fattori che influenzano la calibrazione e la propagazione del suono all’interno del materiale sono la densità, l’elasticità, la
composizione, la struttura e la temperatura del materiale.
Sequenza di calibrazione
Al fine di calibrare correttamente uno spessimetro ad ultrasuoni è necessario procedere secondo una corretta sequenza operativa:
- Verificare la tipologia di materiale costitutivo del pezzo oggetto analisi e reperire un campione di riferimento di valore noto di materiale e condizioni simili;
- Effettuare la calibrazione a punto zero;
- Settare la corretta velocità di propagazione del suono in riferimento al materiale misurato (per questa procedura vi sono apposite tabelle di velocità di propagazione del suono che aiutano a portare avanti l'operazione) o in alternativa, se lo strumento lo prevede, procedere con l’auto-settaggio della velocità di propagazione del suono utilizzando un campione di valore noto tramite apposita funzione dello strumento (questa modalità di calibrazione è disponibile su spessimetro ad ultrasuoni modello VLSTC3000);
- Applicare una modica quantità di gel per ultrasuoni sul campione e verificare ripetibilità e precisione dello strumento su campione noto, in caso di letture errate ripetere i punti 2 e 3.
In caso di settaggio manuale della velocità di propagazione del suono molto spesso è necessario intervenire allo scopo di migliorare la precisione dello strumento effettuando alcune misure di prova e aumentando o diminuendo il valore di propagazione espresso in m/s (metri per secondo) a seconda del valore letto risultante.
Differenza tra calibrazione e taratura spessimetro ad ultrasuoni
Molto spesso vengono confusi i termini calibrazione e taratura associandogli significati pressoché identici. In realtà sono due operazioni che differiscono completamente tra loro. Come esposto nei paragrafi precedenti la calibrazione è un’operazione di “messa a punto” dello strumento, una serie di prove, regolazioni e settaggi dello strumento a parametri ideali per la corretta misura su un dato campione. La taratura, invece, è un’operazione svolta da laboratori abilitati che hanno il compito di verificare lo strumento utilizzando campioni di riferimento certificati (da cui è possibile ottenere una tracciabilità) e documentare tale test con un report scritto. Questo perché ogni spessimetro ad ultrasuoni e relative sonde hanno una deriva nel tempo sia per motivi di usura meccanica che elettrica, per questo motivo è importante che un laboratorio di taratura abilitato verifichi periodicamente che lo strumento si mantenga adeguato per caratteristiche metrologiche all’uso a cui è destinato. La frequenza di taratura, i limiti di utilizzo e le tolleranze di misura di uno spessimetro ad ultrasuoni sono sempre valutati dall’operatore e dall’ufficio qualità i quali stabiliscono inoltre un’eventuale declassamento dello stesso a strumento di seconda linea oppure ne ordinano la riparazione o la sostituzione.
Copyright by © Vulcanoline All rights reserved